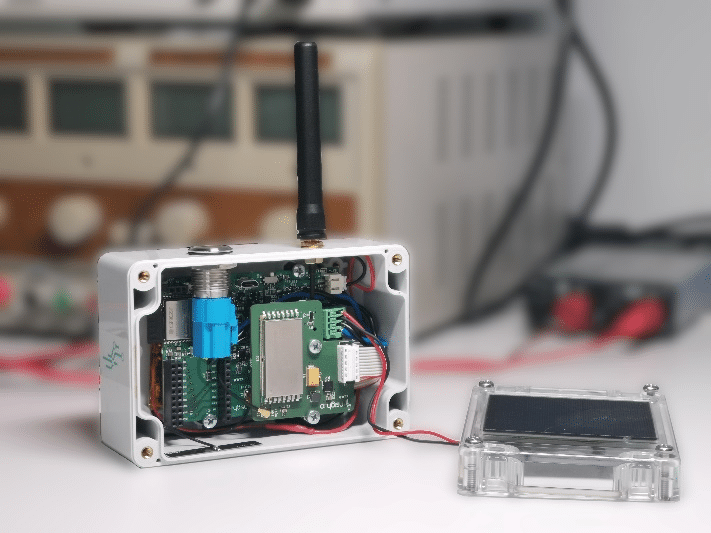
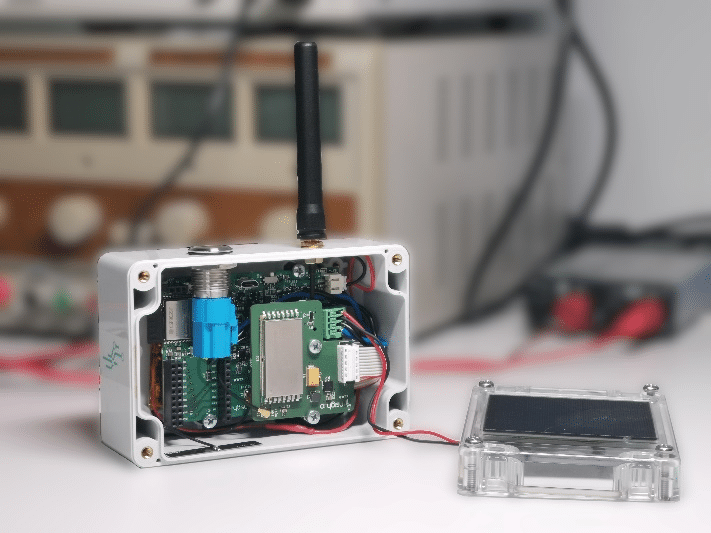
A flexible IoT solution safeguarding hard-to-reach hazardous environments
Empowering operational teams deployed in sensitive spaces with the right sensing and connectivity tools to detect or recover from a possible danger quicker and safer.
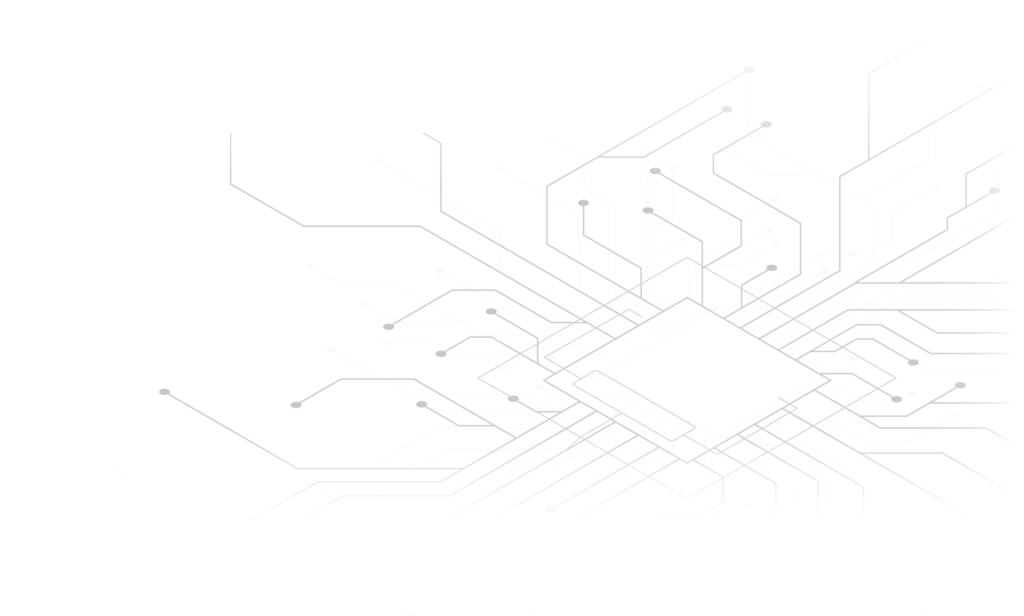
Table of Contents
Introduction
Consider a hostile, hard-to-reach and confined environment, such as an underground tunnel, a mining environment at construction stage or a storage facility used to deposit sensitive chemicals. Such a site may have no pre-existing communications infrastructure, limited or no human access, and possible physical threats to safety and security. Remote teams need a special tool able to autonomously scan the indoor area from a safe distance, detect possible dangers, such as gas leaks or breaches and help on making informed decisions on-site.
System Concept
We introduce an innovative solution that integrates multiple diverse technologies towards a common goal, that is to improve disaster response, through increasing situational awareness. Imagine a confined indoor space which we need to regularly inspect for possible dangers, such as gas concentrations, before entering the site. The site could be in danger due to an unfortunate man-made or environmental event. A control team is located in the entrance of the site. Our proposed approach embeds advanced IoT sensing and connectivity capabilities to unmanned surface or aerial vehicles (UxVs). These UxVs fly autonomously in the space and leveraging the embedded IoT technologies scan the area and report the findings into the control team. After analysing the results, the team can decide the optimal recover measures.
Assuming an unmanned vehicle, e.g. a UAV, from a 3rd party provider, the proposed modular IoT solution includes the following hardware & software elements:
On the hardware side:
- A compact and modular IoT hardware unit that is onboarded on the UAV, and has expansion ports to enable sensing and remote control capabilities in the indoor site.
- Another identical hardware unit that interfaces with a standard computing platform (e.g. a laptop) for implementing gateway/control functionalities from a safe distance.
On the software side:
- Embedded software (firmware) that runs on the IoT hardware units and takes care of low-level communication with the sensors and the radio module.
- Software that runs on the external computing platform and implements high-level gateway functionalities through a user interface, i.e. monitoring the sensor readings and the UAV flight status as well as sending commands to the latter.
Hardware
The hardware elements are developed following the insigh.io modular approach. We reuse our base-board (Link), which is the focal point of any hardware solution built around our tech stack, as it provides a deployment-ready IoT hardware, embedding a powerful micro-controller, versatile power management and expansion capabilities. To accommodate the special requirements of the application we have designed and developed two hardware modules that are attached to the baseboard, enabling:
- Oxygen, carbon dioxide, temperature and relative humidity sensing, based on integrated PCB-mounted sensors. This allows to detect low-oxygen conditions that may be dangerous for the site workers, high-oxygen that may cause a fire, or high carbon dioxide concentrations that are also harmful for humans.
- A fully customized long-range bidirectional connectivity solution based on a low-frequency (VHF 169 MHz) radio module integrating a LoRa chipset. The specific radio module (RFM98W-169S2) is manufactured by HopeRF technologies and integrates Semtech’s SX1276 137 MHz to 1020 MHz Low Power Long Range Transceiver. All communications parameters, like bandwidth, spreading factor, power, coding, etc. are configurable using low-level SPI commands.
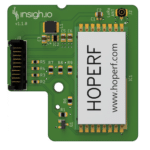
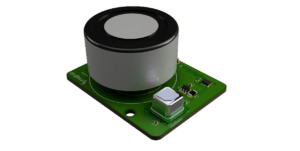
Software
On the software side, there has been custom development of the IoT node firmware for both the UAV and the Gateways nodes along with the design and implementation of the custom UI running in the Gateway.
- The IoT node firmware runs on MicroPython 1.22 and its implementation has been based on the communication scenarios and modem drivers offered by Wei1234c/SX127x_driver_for_MicroPython_on_ESP8266 open-source project, combined with the libraries of insigh.io node open-source project. The node on the UAV, listens to ROS (Robotic Operating System) topics through UART, aggregates data and every 1.5s it generates a 14-byte message with all the required information. The message includes the following information: UAV battery voltage, mean/deviation of latency, 3D position coordinates, as well as insigh.io node Oxygen, CO2, Temperature, Humidity. The message flight time is ~700ms so this gives the opportunity window of 800ms to listen back for commands sent by the Control Gateway. The radio node on the Gateway, decodes messages on reception and sends the data through UART to the computing node (e.g. a laptop) in human readable form, ready to be consumed by the UI. When a command is requested from the Gateway, it is encoded to 1-byte message and is sent back to the UAV for action.
- The Control Gateway UI is a Python application backed by Qt libraries for GUI development (PyQt) and has been tested on Windows and Ubuntu. It offers 5 predefined Control Commands for the UAV, visualizations of the UAV status and finally a clear view of the important sensor measurements. This full bundle of features gives to the operator of the system a clear understanding of the UAV’s environment and a quick access to critical control commands for the UAV operation.
Experimental Evaluation
We have integrated our technology with a 3rd party UAV provided by our partner, VERTLINER. The developed systems has been validated in the Ancient Indoor Mining Sites of Lavrion Technology Park, located in Attica, Greece. The site is currently used for R&D purposes but also as a storage facility for securing sensitive materials (captured gas piles). The demonstration site is accessed by a narrow tunnel entry road. The IoT-empowered UAV flies autonomously through this road, verifying that gas concentration levels met the safety criteria (O2/CO2). Then the ground team can safely enter the site and perform additional operations, such as items identifications, digital mapping etc. In this experiment we were able to understand the value proposition of the proposed solution as well as identify issues for improving it in the near future.
Acknowledgement
Part of the development has been performed in the context of and supported by SECURIT H2020-Innosup-01 EU-funded Project. In this activity we have collaborated with VERTLINER a robotics deep tech startup from Greece and APOGEO SPACE, a space company from Italy.